Husky
2000, 4800
Automated Feeding Systems Built on Dedicated Billet Feeders
This segment of Feedall Automation’s Husky line of parts feeders offers support for billets and similar shaped parts such as shafts, tubes and cut bars with a diameter range within a 2:1 ratio. Both the 2000 series of models and the 4800 Model feature hopper loading—with the parts either bulk loaded or hand stacked in multiple rows when initial part orientation is required or when bulk loading may cause part damage.
Our billet feeders are designed to optimize automated feeding systems with capacity for higher feed rates and gentle handling of parts with lower noise levels. The elevator belt mechanism naturally orients parts as it feeds them, eliminating recirculation of misoriented parts.
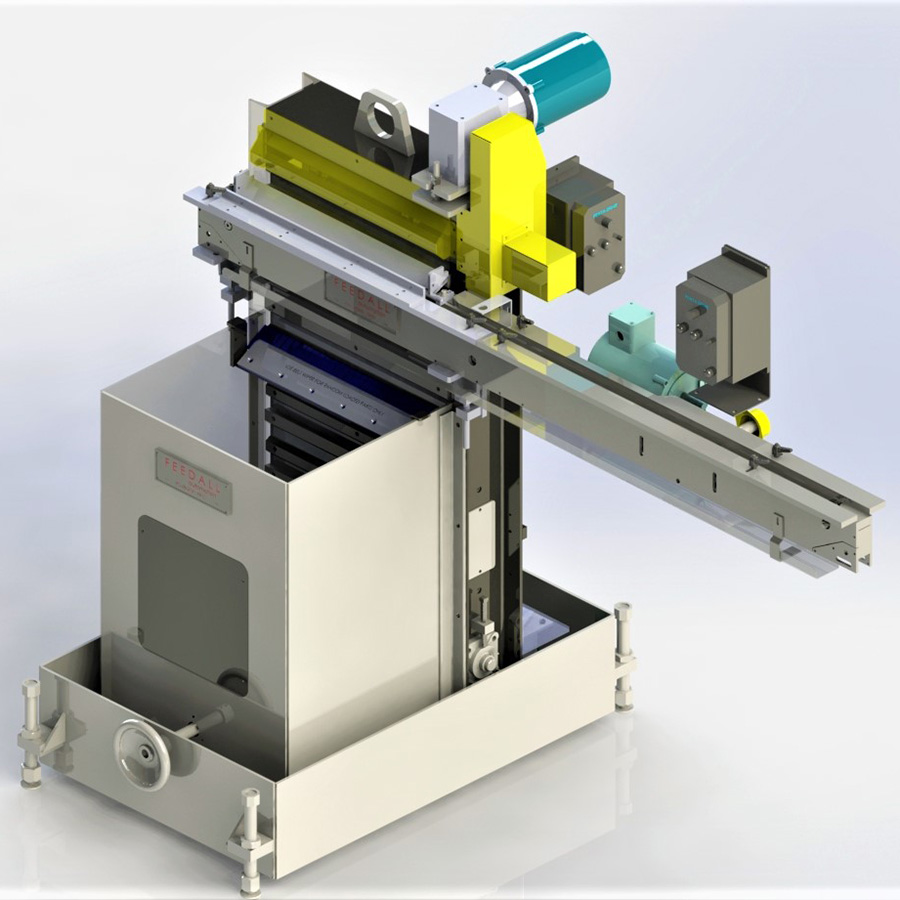
Overview
The Husky 2000 (and its larger variants) are ideal to feed billet-shaped parts to key robot production cells, CNC machining centers, and various types of industrial equipment such as centerless grinders, thread rollers, induction heaters for selective hardening or preheating for forging, and more. Feedall works with you to ensure the billet feeder is sized and equipped with the tooling and options required by your specific application. By seamlessly integrating other automation components, such as mounting our Pointer series conveyors to the front of the elevator, we can create comprehensive automated feeding systems that allow a continuous flow of parts in an end-to-end orientation.
The Husky 4800 is our largest and most robust billet feeder and contains all the same benefits as the 2000, but is built to handle larger and heavier parts—up to 6 inches in diameter and up to 30 inches in length. It is engineered so it does not use vibration or gravity to manipulate part orientation, and features attributes designed to increase productivity and decrease maintenance cost.
- A reversing motor on the cross-feed conveyor for part cleanout or changeovers
- Adjustable or replaceable cleats to accommodate quick changeovers and a broad range of part sizes
- Engineered to accommodate future re-tooling for new parts or programs
- The addition of a metering hopper to take the impact of a full parts dump, increasing equipment operating life
- The addition of a hydraulic tub dumper or motorized roll-over dumper to easily load parts